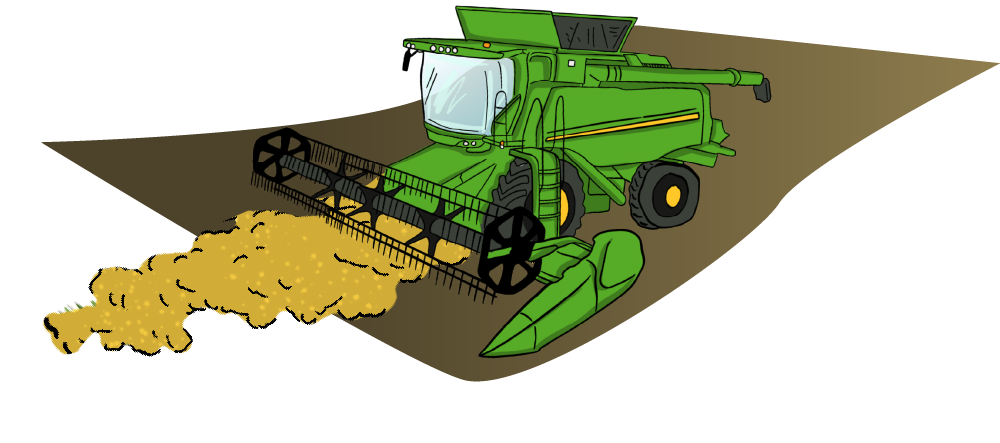
Combines allowed three separate harvesting processes (reaping, threshing, and winnowing) to be done with one machine. Combining all three of these processes led to the name ‘combine harvester’.
A swather is a piece of farm equipment that cuts hay or grain, and drops it into a row called a windrows or swath. The grain is cut so that it can dry out before being harvested. ‘Swather’ is mainly the North American term for these machines. In Australia and other parts of the world, they are called ‘windrowers’.
Cyrus McCormick’s reaper was the first swather invented in 1831. This piece of equipment, along with McCormick’s self-raking feature, allowed one man to cut 16 hectares (40 acres) in a day, which is what 5 men could do by hand at the time.
The first swather could cut 16 hectares (40 acres) in a day!
The McCormick design was then further developed by other agriculture companies. These new designs started to incorporate engines and open cabs which allowed the farmer to ride through the crop and steer while the machine cut the crop and swathed it down.
Open cabs were added to swathers where farmers could steer the machine from.
Modern swathers use a sickle bar to cut the stems of the crop. A reel helps the cut crop fall neatly onto a canvas or auger conveyor which moves it and deposits it into a windrow or swath, with all of the stems pointing in the same direction. Because of the swather, the combine is able to do its job of picking up and separating the crop from the chaff easier.
New swathers are equipped with technology that allows farmers to map out their crop, cut the stalks evenly, as well as turn on ‘autosteer’ so the swather will drive itself up and down the field.
Swathers cut down the crop and drop it in a row so the grain can dry out before it is harvested.
Aside from the addition of closed-cabs, engines, and computers, many of the original design elements remain on modern swathers today. You see the large headers with rakes to pull the crop in, as well as the machines’ ability to lay the crop down in a straight row after it’s been cut.
Swathers eventually replaced the binder and combines replaced the threshing machine.
Modern swathers have closed-cabs so the driver is protected from the noise and dust.
Combines were a major improvement in equipment used for the harvest season. The early farmers would harvest their crops by hand. Grain or hay was cut with a scythe and left to dry in the sun. A cradle scythe (also called a hand cradle) cut the hay and dropped it into piles. The grain was left to dry out and then farmers would separate the kernels from the chaff by hitting the stalks with a wooden flail. This would allow them to winnow the grain to separate the kernels from the chaff.
This is the original process it would take to harvest crops by hand.
The early combines were pulled by teams of oxen or horses. These were known as threshing machines! They were very big and usually needed a group of men to operate them. In the early 1900s, men would get together and create threshing crews of up to 30 workers. These crews would travel around and help farmers harvest their crops.
Threshing machines were the main piece of harvest equipment and the designs continued to evolve. Eventually, tractors replaced the need for oxen or horses. Because of improvements to the threshing machine, we have combines as we know them!
These farmers are pulling the threshing machine with a group of mules.
The threshing machine would stay in one section of the farm field and the cut grain would be hauled in grain carts to the threshing machine to be harvested.
The first combines were built in the United States in the 1850s, where they would reap, thresh, and winnow in one process. In the 1870s, combines were used in California and that state became the headquarters for combine production and distribution. Those combines needed some improvements to successfully combine crops on the Prairies.
The first combine was brought to Saskatchewan in 1910 to harvest. Although this combine was very simple compared to modern harvesting practices, it was a big step towards the mechanization of farming on the Prairies!
This is one of the early combines from 1927, where one person would drive while another would have to bag the grain.
Combines have since grown to include a variety of engine sizes, hopper sizes, and other technology. The computers included in combines allow farmers to watch the levels of moisture in the crop, the yield that the combine is harvesting, and much more!
There have been improvements to the combine over the years that have made it much more efficient.
The evolution of combines has reduced the amount of manpower required and sped up the harvesting process. Some farmers can recall what it was like combining 40 years ago with an open cab where it was dusty and noisy. Many improvements have been made to the combine!
Modern combines have made the harvest process much faster!
Learn how a combine works by diving in and seeing the inside of a combine in action.
Combines are used to harvest most crops. In order to do this, special headers were designed for specific crops. Straight-cut headers are the large implements that attach to the front of the combine and will cut the crop and pull it into the combine.
The combine headers are attached to the front of the combine and they cut or pick up the crop and pull it into the combine.
Straight-cut headers (also known as draper headers) have belts that feed the crop to the centre, where it is pulled into the combine. These headers cut the crop and harvest it at the same time, which means that a farmer doesn’t need to use a swather to cut the crop first. This saves a lot of time for farmers!
In order for a crop to be straight-cut, it has to be sprayed with a desiccant. The dessicant will kill the crop (and any weeds) so it can dry out the crop more quickly and evenly.
Straight-cut headers cut the crop and harvest it at the same time!
Corn headers are built specifically for harvesting corn. They have cones that stick out and fit between the crop rows. There are gather chains between the cones that pull the stalks back and cut them with 2 knife rolls. The stalks then fall to the ground and the heads of corn are fed back into the auger.
Straight-headers cut the crop and harvest it at the same time!
Auger headers (also known as pick-up headers) are used to pick up swaths. The belts turn, picking up the swath, and then the auger takes it through the combine to be threshed.
There is a large auger that pulls the crop into the combine on pick-up headers.
The advancements of the combine harvester have made harvest much more efficient. This is important because some years the hot, dry weather that is perfect for harvest lasts only a few weeks in fall.
The interior of combines has also evolved, and the farmer has a great view of what is happening on the combine header.
This is the view that farmers have of the combine headers while they are combining.
The methods of storing grain have changed a few times over the years. The first style of grain storage was wooden bins. These bins were smaller in size (approximately 3.6m x 3.6m x 3m) and could hold about 27 tonnes (1,000 bushels).
Early farmers used wooden bins to store grain.
Next to be designed were round steel bins. They had flat bottoms so farmers would have to shovel out all the grain. These bins could hold about 13 – 190 tonnes (500 – 7,000 bushels) depending on the size. Shovelling bins is a very hard job. It is warm in the bins and the dust can be very itchy and dusty, which is not great for a farmer’s health.
Flat bottom bins better protect the grain but were still difficult for farmers to empty.
Soon, round steel bins with flat bottoms were further developed to add hopper bottoms, which was a triangle-shaped bottom that would allow the grain to fall towards the bottom and into an auger. This invention meant that farmers would no longer need to shovel the bins, saving them time and keeping them healthier!
Modern hopper bottom grain bins are shaped so the grain drains to the bottom. Because of this shape, farmers don’t have to shovel grain into augers to remove the grain from the bin.
Farmers use grain aeration systems to control the temperature and moisture level of the grain in the grain bins. Through aeration, the air is forced through the stored grain in grain bins at a low rate to remove any heat and moisture in the grain and to maintain its quality. Grain aeration allows farmers to harvest their grain before it is dry in the field (or at a safe moisture content) and then dry out the grain in the bin.
The grain aeration process uses large fans to control the temperature and moisture of the grain being stored in grain bins.
Another way that farmers may choose to store grain is in grain bags. These are large, white bags that hold between 10,000 and 15,000 bushels depending on the size. The grain is augured in and out, requiring very little manual labour. Grain bags are usually used when farmers do not have enough bin storage on the farm.
Grain bags are mainly used when a farmer has run out of grain bin storage.
As farmers were beginning to see bigger harvest yields, the innovation of moving grain began. Originally, farmers hauled their grain with wagons and carts that were pulled by horses. This changed once the gasoline engines were invented and farmers were able to move grain with vehicles known as grain trucks.
Like all the other farm equipment, grain trucks continued to change and farmers began using semi-trucks and large trailers. This allowed them to move more grain faster and more efficiently. Today, you will see farmers using a mix of older styled grain trucks and semis with trailers.
Semi-trucks are commonly used on modern farms to haul grain.
This combine is dumping grain into the semi-truck to haul it to an elevator or a grain bin so it can be stored.